Well, I've finished uni. Not just this year, but my whole degree, which is kinda scary!
With honors starting next year, I've got about 4 months up my sleeve to flit away, so what better passtime is there than making bows?
This thread will be a buildalong of two, maybe up to five, bamboo backed longbows that I'm trying to get finished ASAP.
The bows are all Ironbark, though I'm not quite sure of the variety more accurately than that. The bamboo is Moso.
Before I make a bow, I always do a bend test to find the modulus of elasticity and modulus of rupture (actually a bit below this figure), and with these figures, do some computations to give me dimensions down to .001mm accuracy for bows which have equal stress along their length.
Perhaps the most important thing in doing a bend test is the accuracy of measurement of your test board.
Here is my test board. It measured 320x27x4mm.
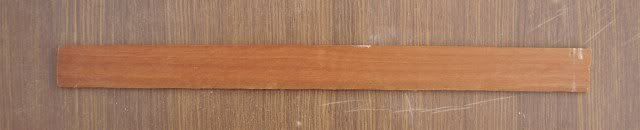
For those that have read TBB, you may not recognise my bend test. Tim Baker used a cantilever bend test, and mine is known as a simple supported beam bend test.
It's a fairly simple affair: the board is supported at either end, with a weight hung from the middle. Here is my setup. The board accross the top with the paper taped to it is for measuring and recording the deflection. It's also important to accurately measure the distance between the supports.
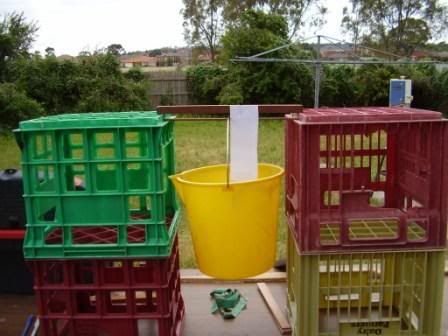
Into the bucket goes dumbell weights, usually 1kg at a time. At each KG, I put a mark on the bit of paper where the test board has deflected to. Then I remove the wieght, and see if the board has taken a set. Here is the beginning of the process:
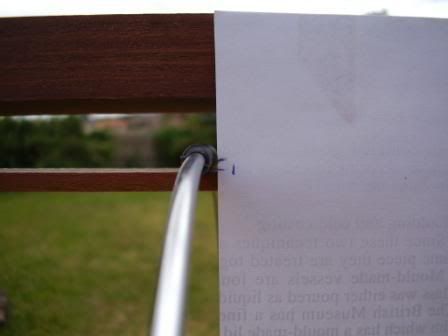
The black mark shows where the board started.
After 7kg, the board was not taking set:
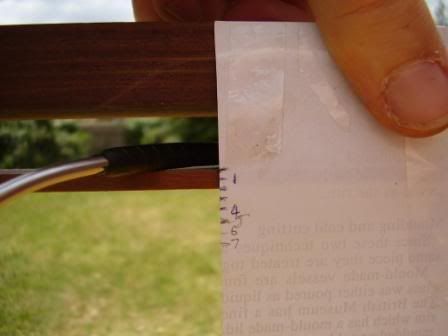
The board did take set at 11kg, and broke at 13. I'm on a pc at uni, otherwise I'd have given all the measurements. Anyway, the numbers I got allowed me to calculate the figures on stiffnes and rupture, which I probably aslo should have brought along to share. Maybe next time.
Anyhow...all the numbers i got were put into my special computer, which gave me the dimensions to work this wood down to to get a given draw weight at a given draw length. I'll have to share those next time too, but you should be aware that those numbers will only work with this bit of wood that I have, as all wood has different mechanical characteristics. Both of these bows will be just under 50lb @ 28" when done. As these bows will be reflexed and bamboo backed, I computed these bow blanks to be about 37lb @ 28", as the bamboo and perry reflex will raise the draw weight.
So here is one of the three boards, which I will resaw on my bandsaw into two, then glue on risers.
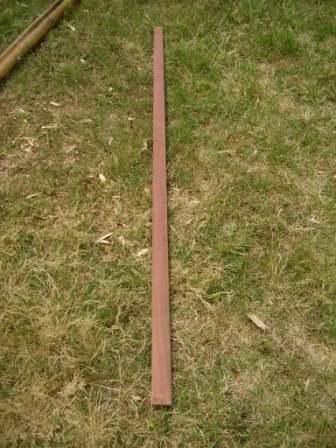
Here it is sawn. Wasn't that quick!

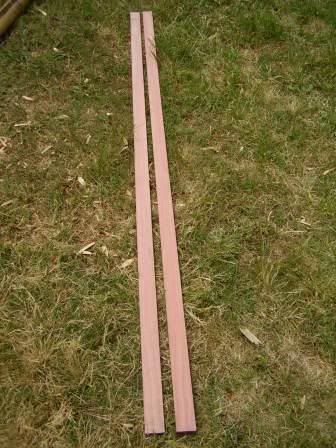
I printed out a full scale schematic of the bow's shape, stuck it on the boards, traced around it, then cut it out. Here's yours truly using the finger-removing device to cut the front view shape of the bow blanks. I don't care how stupid I look wearing the safety equipment...I like looking at stuff and I enjoy music.


Here are the bow blanks cut to front view shape. The pic may not be very clear. I won't cut the handle shape until the riser is glued on, but I have marked it out.
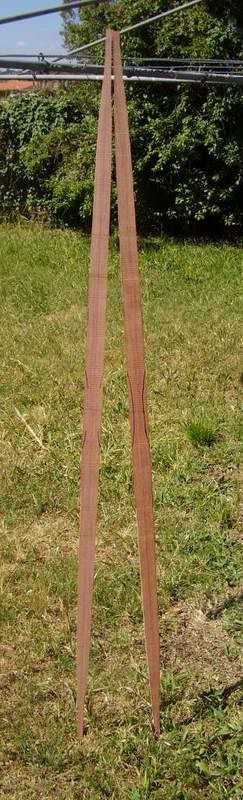
So there they are, ready for smoothing, risers, and backing. I also have to taper the thickness, which I will likely do with a stanley surform, spokeshave and scrapers.
The next step is to get some bamboo ready. Actually I did the bamboo first, but you won't know that coz of the order I've told you and shown the pictures in! The bambo is a 6', 4" pole from bunnings. I chose one that was uniformly round, thick walled, and not already split, with as little taper as possible along the length. Another requirement is that the nodes should be evenly spaced along the pole, as many have the nodes bunched close to the ground, and far apart at the top.
I'm splitting it from the thick end with an original bowie and a plum mallet.

I do it by splitting along one line: the pole has a split down one side but is still whole, and then split the width I need out from the pole. Here it is:
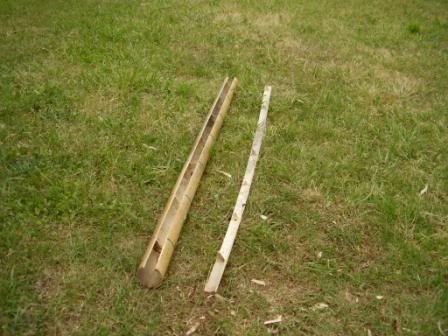
Witha quick turn on the bandsaw, the insides are flattened, but not fully thinned. I tried to do it all on the saw once and ruined the backing, so now I'm a bit more careful.
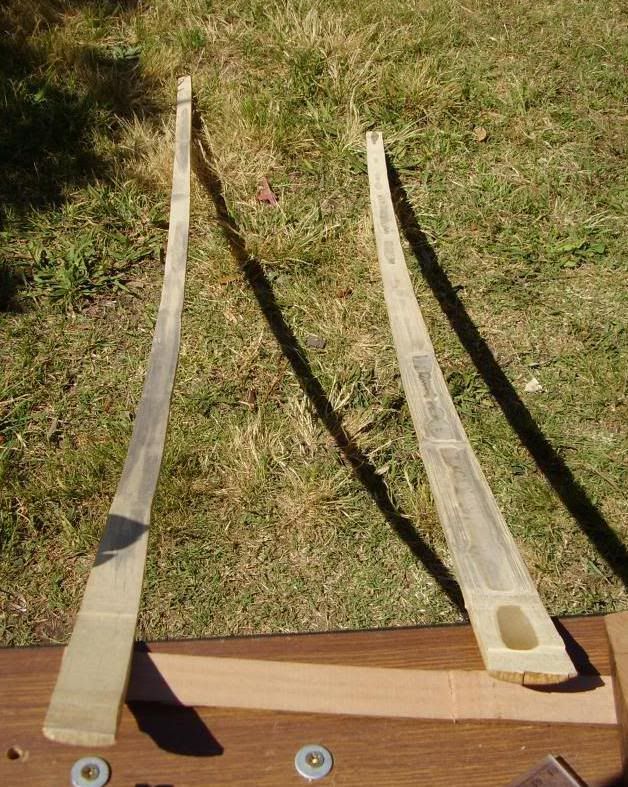
That's as far as I've got so far. If the rain hold off I'll be doing a lot more on them today, which means more pics in the next few days.
Feel free to ask any quetions, as I'm positive I haven't explained everything well enough.

Cheers,
Dave[/img]